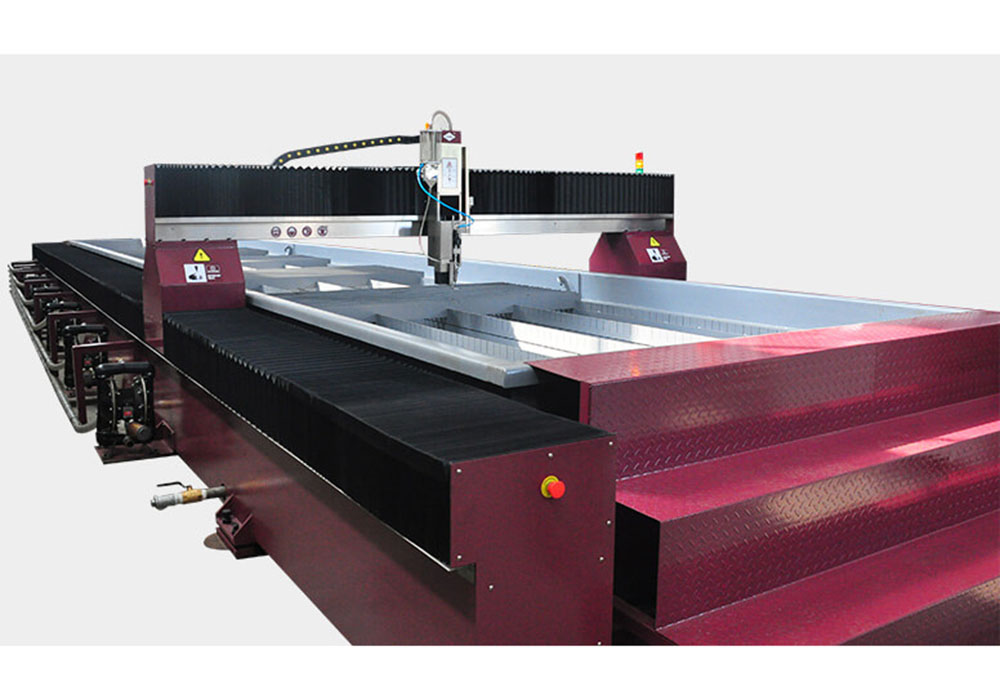
The use of abrasives in water jet cutting machine increases the complexity of the system, thereby increasing the risk of failure and subsequent downtime. However, with appropriate precautions and maintenance, you can greatly reduce the possibility of water jet cutting machine.
Using inferior abrasives is one of the main causes of water jet obstruction.Many cheap abrasives cannot meet high manufacturing standards like high-quality abrasives,and many contain contaminants that can clog the water jet cutting machine.So buy abrasives from reputable sources to make sure they are high-quality products.
2.Take precautions to prevent debris from entering the hopper
Even small debris can clog your machine,so take precautions when loading into the hopper to ensure that nothing else enters the mixture.
3.Always keep the abrasive dry
Do not expose abrasives to high humidity environments for a long time,the high moisture content in abrasives can make the machine feed system difficult to handle.When not in use,please make sure that garnet abrasives are always stored in a cool,dry place.
4.Ensure your abrasives feed rate matches the orifice and nozzle size.
Before cutting,make sure that the abrasive feed rate set on the cutter is correctly matched to the orifice and nozzle size you are using.Different orifice and nozzle sizes have different abrasive requirements.When the feed speed exceeds the abrasive consumption speed of the orifice and nozzle,clogging occurs.
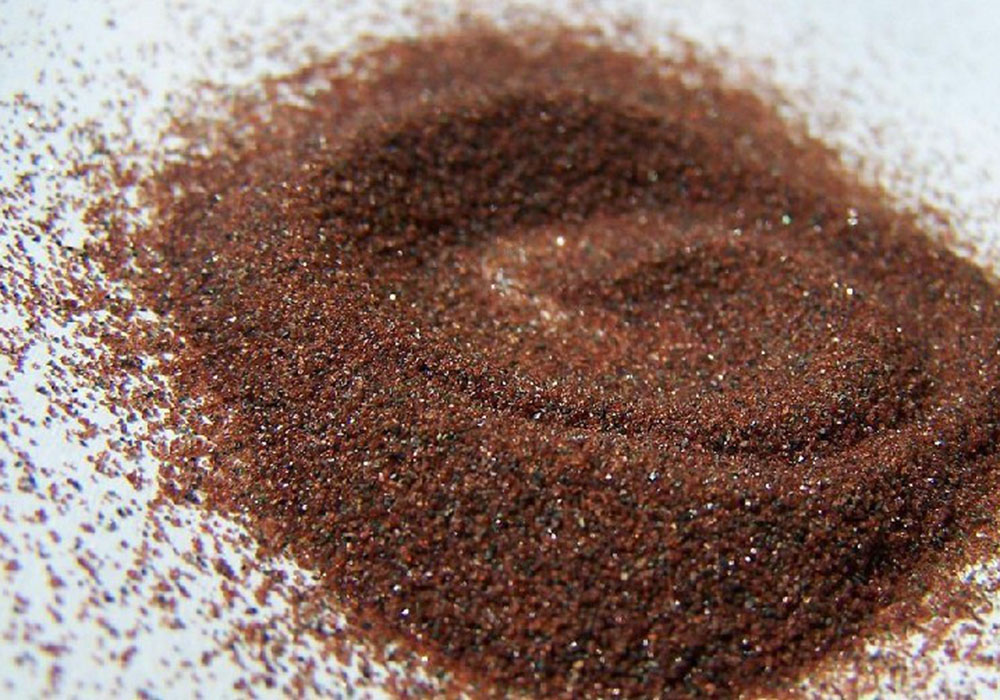
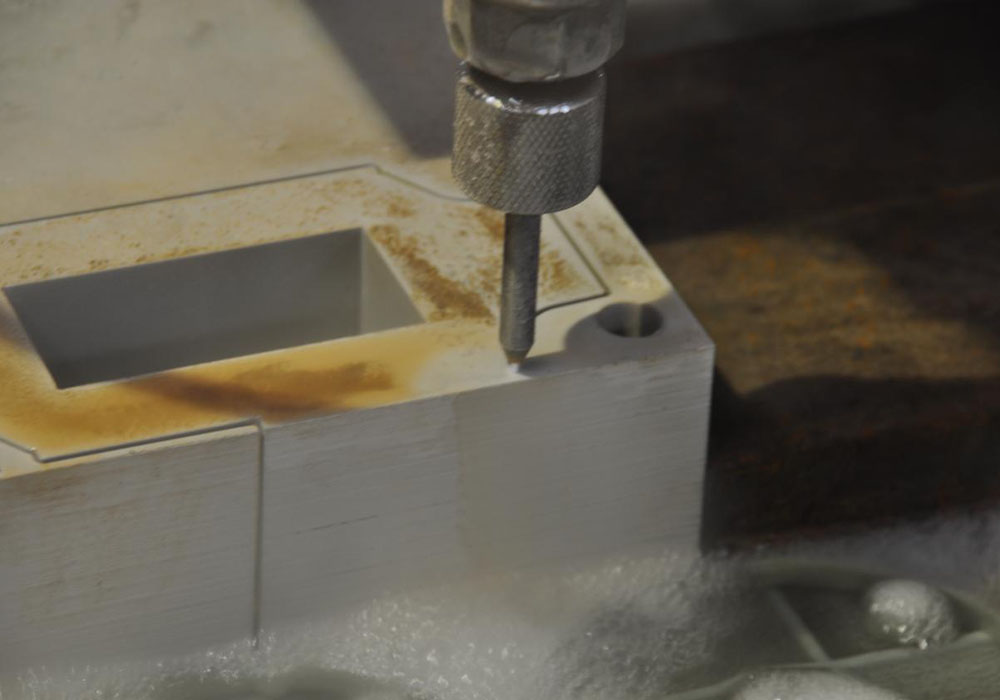
If the orifice and nozzle are not used properly,you will put the water jet cutting machine at risk.If one of them does not match its similar products,clogging may occur.Before cutting,please contact your supplier to make sure you have the correct combination.
6.Keep proper cutting distace
If you touch the material with the tip of the nozzle.When this happens,you will have excessive back pressure on the abrasive flow,which will cause the abrasive to become wet and track your production line backwards.You need to maintain the correct distance from the nozzle to the material being cut.
7.Replace worn orifices
One of the easiest way to prevent clogging of the cutting system is proper maintenance.Part of the maintenance work is to replace worn parts,especially the orifice,which has a higher wear rate than other parts on the machine.Check your water jet cutting machine regularly to prevent long downtime in the future.
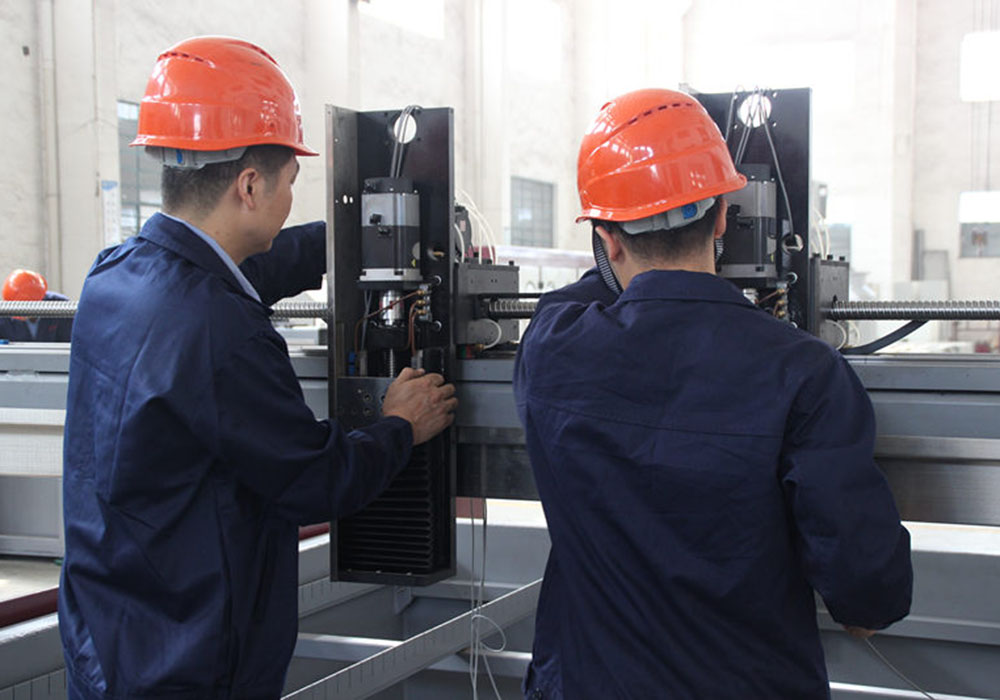
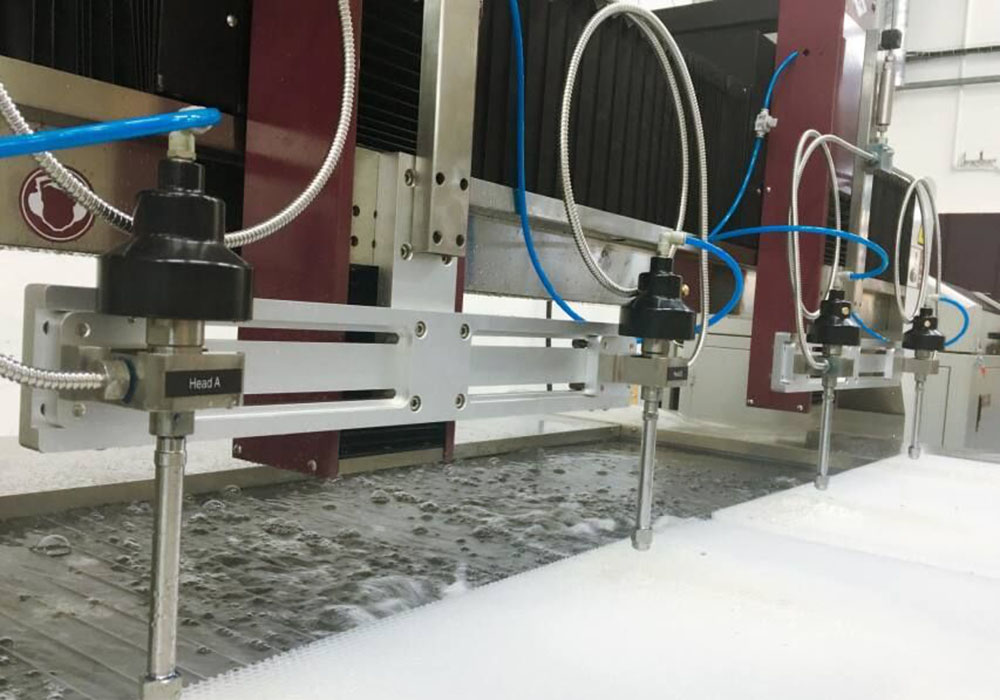
Familiar with your machine manual can prevent many problems in the cutting process. Each machine has different maintenance intervals,parts and components,and long-term operation requirements.Take some time to understand your individual machine's manual,and you will get more uptime.
9.Operators should be properly trained
Operating a water jet cutting machine is not simple,especially when you are add abrasives to the mixture.Anyone who operates a water jet cutting machine needs to receive proper training to ensure that the machine runs as safely and efficiently as possible.