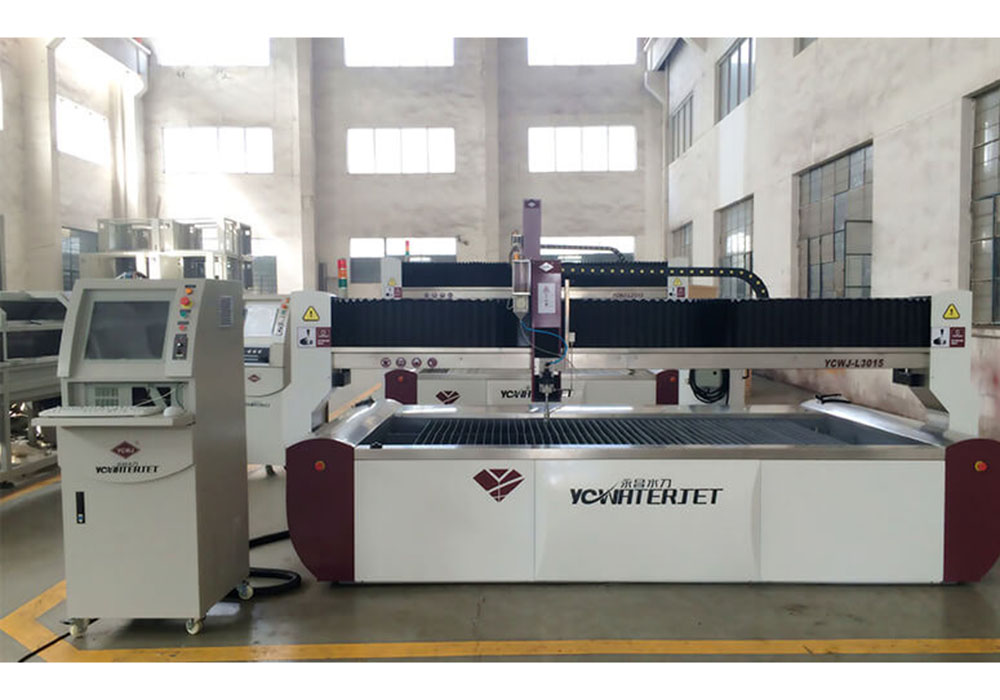
2. Cutting head. A long enough pipe can ensure complete mixing of abrasive and compressed air, thereby forming a consistent and orderly cutting stream. Experience has concluded that the ideal pipe length should be 3-4 inches. It is very important to ensure the accurate connection and perfect cooperation of every spare parts of waterjet cutting machine,which can minimize the damage of high pressure water jet to consumable parts.It is worth noting that with the increase of nozzle diameter,the cutting depth decreases.However,when the nozzle diameter is reduced under a certain pressure,the water jet close to the nozzle will be atomized due to the entrainment of air, which will make it lose the cutting ability. Experience has concluded that the outlet diameter of the nozzle for waterjet cutting is recommended to be selected within 0.1~0.3mm. The proper distance between nozzle and the surface of the material will reduce the loss caused by the water jet when it passes through the air.It can maximize the cutting efficiency.Besides,if the distance water jet needs to pass through the air is too long,the water jet will be blocked and diffused.
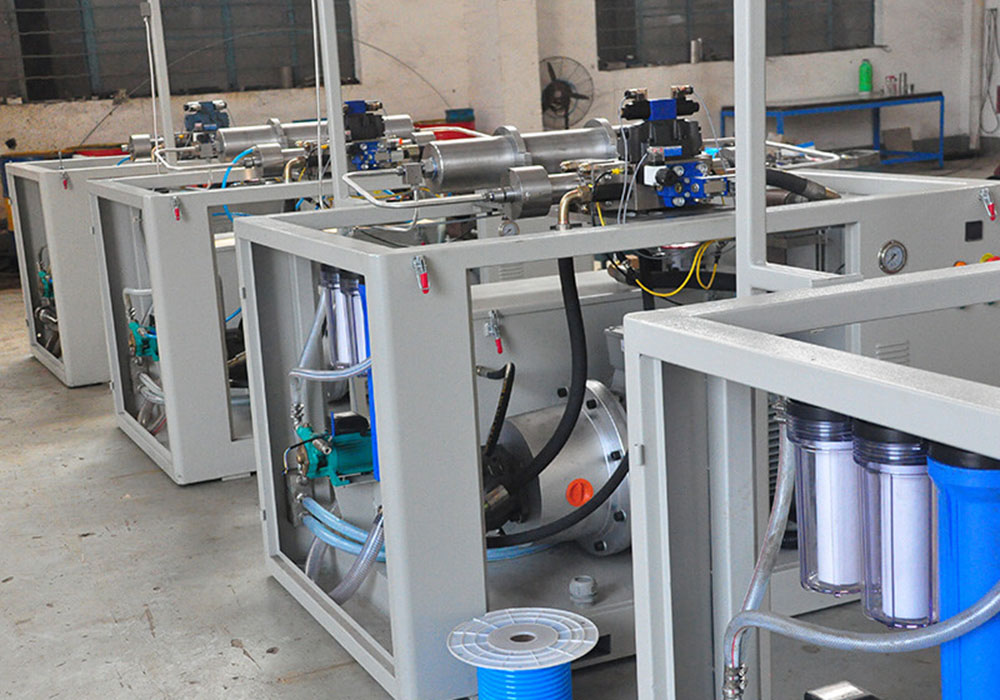
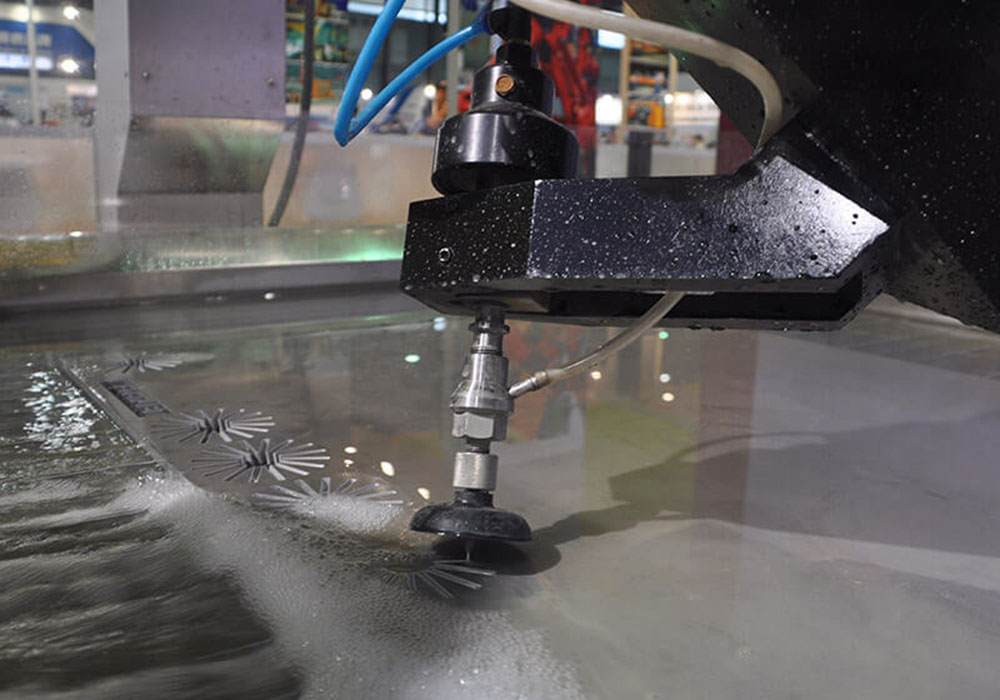
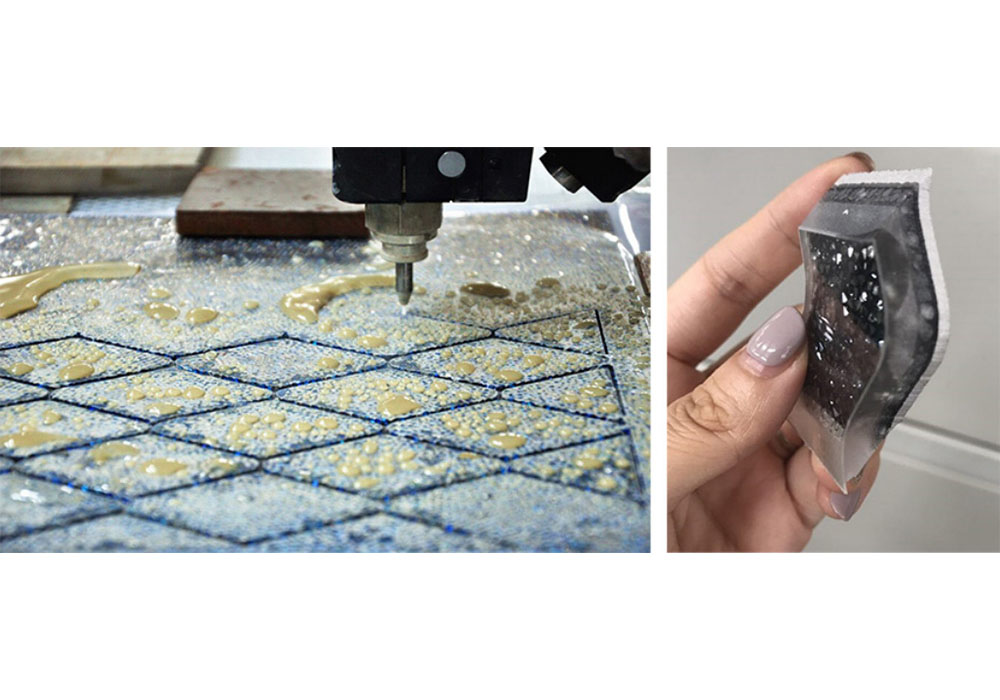
4. Experiments prove that waterjet cutting machine with different abrasives can cut materials with different results.The maximum depth of the structural steel plate is cut by garnet and silicon carbide abrasive.At the same time,with the increase of abrasive flow rate,the crowded abrasive particles will cause interference between abrasive particles.So the effective number of impacts will decrease.There is usually an optional bearing capacity.When the abrasive flow rate is low,the cutting depth decreases.